【方式別紹介】3Dプリンタって何?ここから始めよう3Dプリンタ
おはようございます、こんにちわ、こんばんわ
前回の予告通り、現在市場に出ている3Dプリンタの
造形方式や特徴なんかを私なりにまとめて
ご紹介していきたいと思います。
以前の記事でも触れましたが、
”3Dプリンタとは何か”ということに立ち返りましょう。
3次元的なデジタル・モデルをもとにして、
(現実の)物体をつくりだすことができる機械のこと。
日本語では(あまり一般的ではないものの)
「立体印刷機(りったいいんさつき)」と、
漢字表現で呼ぶこともある。3次元モデルをもとにして、
現実の立体物を出現させる機械のことである。
普通のプリンターのように、紙という
平面(二次元)の表面にインクをのせて
「(二次元的な)絵」として描く機械とは異なる。
また、立体物を出現させる手法としては、
なんらかの方法でメス型を作っておいて
そこに造形材を充填、固化させて作る技術があるが、
3Dプリンターはそうした手法とも異なるものである。
wikipedia 3Dプリンター より抜粋
ということで毎度恒例、ウィキ先生からの抜粋でした。
最後の1文にありますように、
従来の手法とは異なる手法で立体物を作る機械です。
3Dプリンタは、初期は1980年代に開発・実用化されていましたが、
大変高価で特殊な制御を必要とするものでした。
2000年半ば頃までは、数百万円規模の投資額が必要なため、
大手企業の事業所で導入されることが主でしたが、
2008年以降は数十万円~数万円の3Dプリンタが市場に出始めことで、
中小企業や個人でも導入されるようになりました。
従来の切削や鋳造、射出成型との比較すると、
3Dプリンタでは型や治具の作成が不要という点から
設計段階での試作において、早急に現物を確認したい場面や、
医療現場で患者一人ひとりに合わせた一点モノの製造、
航空宇宙分野で従来手法とコスト差が大きくない場面に向いています。
「製造する」という側面でみる3Dプリンタのメリット
・切削加工では難しい中空形状や、複雑な内部形状を造形できる。
⇒中空構造を容易に作成できるため、部品の軽量化等もできる。
・各部品ごとに製造するのではなく、組み立てた状態で造形できる。
・複数の異なる材料を使用して一体物を造形できる。
・再現性が高い。(誰が何個作っても同じ物が作れる)
・複数のモデルを一度に造ることができる。
「操作する」という側面でみる3Dプリンタのメリット
・操作者の技術力に依存しない
・機器の取り扱いが容易で、造形中に人手をあまり要さない
(作りたいデータを機械へ読み込ませればスタートを押すだけで良い)
デメリットは
・現状では大量生産への適応が難しい
⇒基本的に従来手法と比較して材料費が高価であったり、
1個あたりの造形速度が遅い
・要求される精度が高くなると製作時間が増加する
⇒層の厚みが精度に直結するため
・強度を求められる部品への適用が難しい(FDM方式)
⇒使用可能な樹脂の制限や層間の剥離の問題
以上が従来の製造法・加工法と比べてのメリット・デメリットです。
やはり試作時に用いる機械という印象が色濃くでている様に感じます。
上記で出てきましたが、「設計段階での試作」の手法として
「ラピッドプロトタイピング(RPと略します)」があります。
外観や性能評価を行う為に試作品を製作します。
その際は量産品と同じ材料を使うほか、クレイモデル(粘土)、
モックアップ(木材)での製作が主でした。
ですが、製作用の型を作ったり、削り出しで製作したりと
試作品製作に掛かる時間とコストが大きな負担となっていました。
近年はコンピューター技術の発展によって、
製品のデザインや機構を3Dで設計するようになりました。
そのデータを使って、コンピューター上で
解析・シミュレーションが可能となったことで、
試作品を製作しなくても事前評価が可能になりました。
しかし、人間の視覚、触覚、嗅覚など定量化が難しい項目については
解析やシミュレーションでは完結することが難しい為、
引き続き試作品の製作は必要とされています。
とはいえ、製品開発サイクルが短期化しており、試作品の製作期間も
短縮する必要があります。コンピューター上で事前評価が
可能となったことで、試作品での性能評価のニーズが下がった為、
形状のみを早期に作成する手法として
ラピッドプロトタイピング(RP)が登場しました。
このRPでは「積層造形法」と呼ばれる製造手法が用いられます。
造形したい3Dデータを一定の厚みで何層にも輪切りにした
データを作成し、それを元に紛体・樹脂・鋼板などの材料を
2次元加工したものを何層にも重ねて立体物を製作する手法です。
「積層造形法」を細かく分類すると、以下の5種類に分かれます。
光造形法
紫外線を照射することで硬化する液体樹脂を用いた造形法。
初期のRPはこの手法から始まった。
元々は高価な機器が必要であったが、液晶パネルの透過光で
直接硬化させる方式では近年5万円を切るモデルも販売されている。
粉末法
素材粉末を層状に敷き詰め、高出力レーザーなどで直接焼結したり、
インクジェット方式で接着剤を添加し固めたりする造形手法。
前者は青銅、鋼、チタンなどの金属系材料で用いられる。
後者ではスターチ、石膏などの材料で用いられる。
ランニングコストを抑えた3Dプリンタに利用されることが多い。
フルカラー印刷に対応しているのも特徴である。
熱溶解積層法(FDM法)
熱可塑性樹脂を高温で溶かし積層させる造形手法。
RP・3Dプリンタとしては唯一、本物の熱可塑性樹脂を使用でき、
ABSなど様々なエンジニアリングプラスチックを使用できる。
元々、アメリカのメーカーがこの方式の特許を持っていたが、
基本特許が切れたことで、この方式をつかった安価な機器が
販売されるようになり、個人用の普及が加速した。
樹脂を熱で加工するという特性上、造形物が反って変形するなどの
トラブルが多く、使いこなすにはある程度の慣れが必要である。
シート積層法
シートを積層させて形状を作る造形手法。
数種類あり、カッティングプロッタで切り込みを入れた紙を
糊で積層する方式や光硬化樹脂をシートにインクジェットで
出力してから転写する方式や水溶性の紙に熱硬化性樹脂や
光硬化樹脂のモノマーをしみこませて一層の積層毎に
加熱または紫外線照射、加圧して硬化する方法がある。
粉末法の基材をシートに置き換えたもの。
インクジェット法
液化した材料、又は接合剤を噴射して積層する造形手法。
インクジェットプリンターの原理を応用している。
カラーインクを混ぜた接合剤を用いたカラー造形物も作成される。
液体状の光硬化樹脂を噴射後、紫外線光を照射して硬化する方法や
ワックスを噴射する方法などがある。
材料の無駄が少なく、歯科技工や宝飾品に使用される
ロストワックスの原型のように比較的精密なものを作るために適する。
オーバーハングの部分のために水溶性のサポート材を出力したり、
複数の素材を造形物上で混合することで透明度や柔らかさを
変えられるもの、フルカラー出力に対応した機種もある。
上記手法で見たことある単語があった方
今までの記事を読んだ方 or 3Dプリンタに造詣がありますね?
熱溶解積層法(FDM法)はS5の紹介で、
インクジェット法はアジリスタの紹介で出てきましたね。
既に文字数が多くて読むのが億劫なレベルですので
記事を分けて各方式の機種紹介や細かな特徴紹介をしていきますね。
【方式別紹介】第1弾はこの辺りにしましょう。
次回もお楽しみに!
ご愛読、ありがとうございました。
By M.I
次の記事はこちら
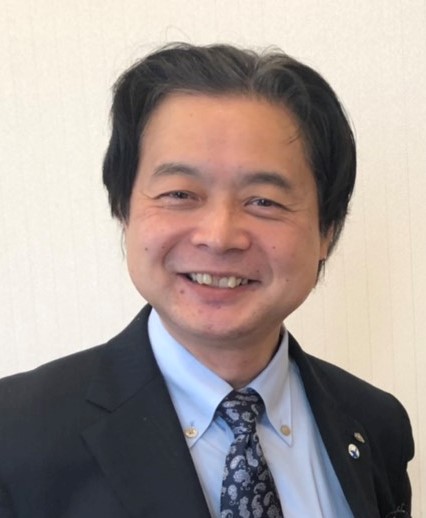
岸 竜也 (きし たつや)
株式会社キシテック 代表取締役
3Dプリンターを使ったモノづくりを提案しています。
機械設計を生業としてきたため、設計力に自信があります。
様々な分野から、試作品等の依頼を受け、製品化のお手伝いを多数してきました。
手書きの絵から、3Dデータを起こして、3Dプリントすることも。
自身も設計のみならず、機械加工、機械板金加工、溶接などのモノづくりを経験してきた実績があり、いろいろモノづくりを相談出来ます。
現在は石川県工業試験場様や、ISICO(石川県産業創出支援機構)様、JAIST(北陸先端科学技術大学院大学)様、石川工業高等専門学校様などと、繋がり多方面での対応が可能です。