ネジ作成も朝飯前!アジリスタ3100での造形精度は0.02mm!
本日ご紹介するのは、弊社のメイン造形機「アジリスタ3100」での造形例です。
その前に、アジリスタ3100について知りたい方はこちらのブログをご覧下さい。
今回作ったものは「M8のネジ」です。
え?ネジ?今更?と思われた方は先ほどのブログや弊社のギャラリーを見てくれてる方ですね。いつもありがとうございます。
はい。改めてネジの出力をしてみました。
ですが、ただ出力するだけはすでにやっているので、今回やったのは
サポート付着部のモデル縮小に対してデータ側で何ミリ肉盛りするのが良いのか?
という実験です。
アジリスタでは、造形時にモデル材とサポート材をインクジェットヘッドから塗布しながら、同じくヘッドに搭載されたUVランプで硬化させ、積層造形しています。
サポート材が付着している部分は付着していない部分と比べて、若干造形物が痩せてしまう(小さくなる)ため、見た目に分かるくらいの段差が生じる場合があります。
このあたりのお話はこちらの記事でも触れていますので、よかったらご覧ください。
サポート材によるモデルの変化を避けるため、外装に来る面や勘合部などはサポート材が付着しないよう造形する。
または、完全にサポート材に埋まった状態にすることで、段差やデータとの差異が出ないようにするといった手法を取ります。
今回のM8のネジでは、ボルト側、ナット側共に、ネジ山がサポートに埋まった状態で造形されるため、作成データと比べて勘合部の隙間(遊び)が若干大きくなります。
隙間が大きい=ガタツキが大きいため、ネジを締めこんでも上下左右にカタカタと揺れてしまう可能性があります。
なので、造形データの時点で、標準のネジ山よりも大きいものを作っておくことで、サポートによるモデル縮小でのガタツキを抑えよう!という実験となります。
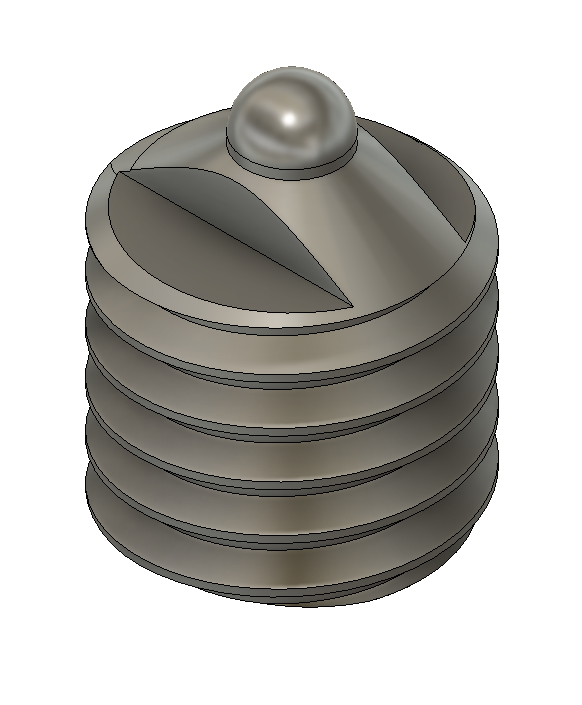
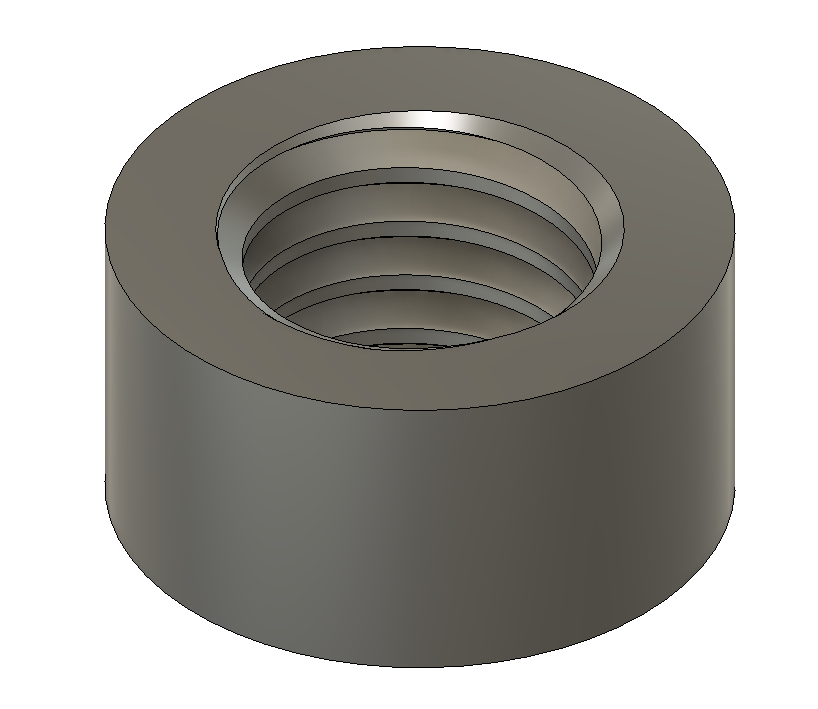
まずは、CADでM8ネジのデータを作成。
ボルト側は高さ約10mm。ナット側は高さ6mmで作成しています。
データ上でのネジ部の断面はこんな感じです。
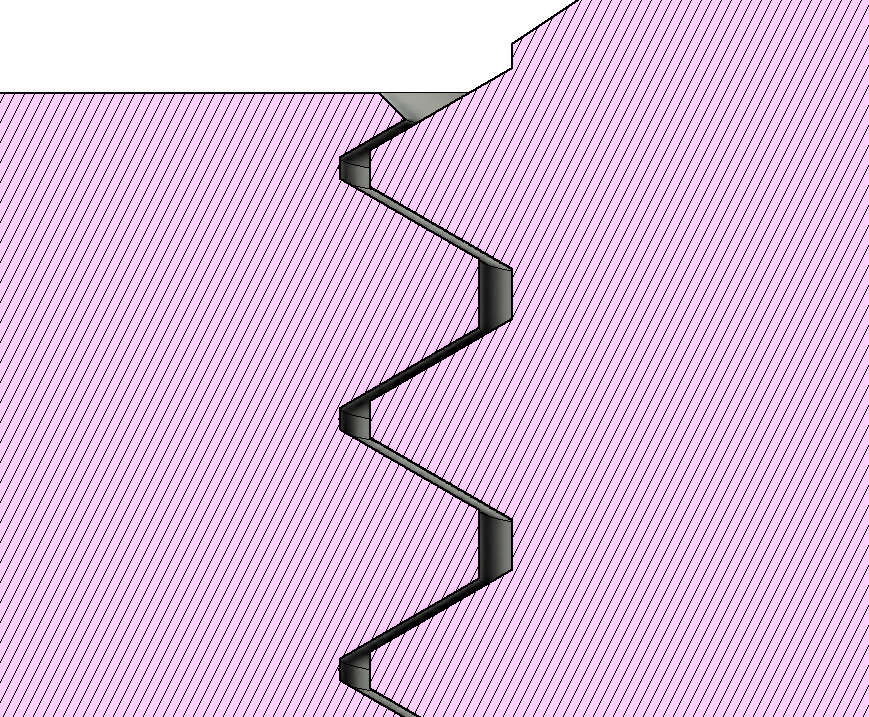
標準データにおける山谷の隙間は最大で約0.08mmほどでした。
画像ではほぼセンターに合わせてあるため、片側0.04mmほどです。
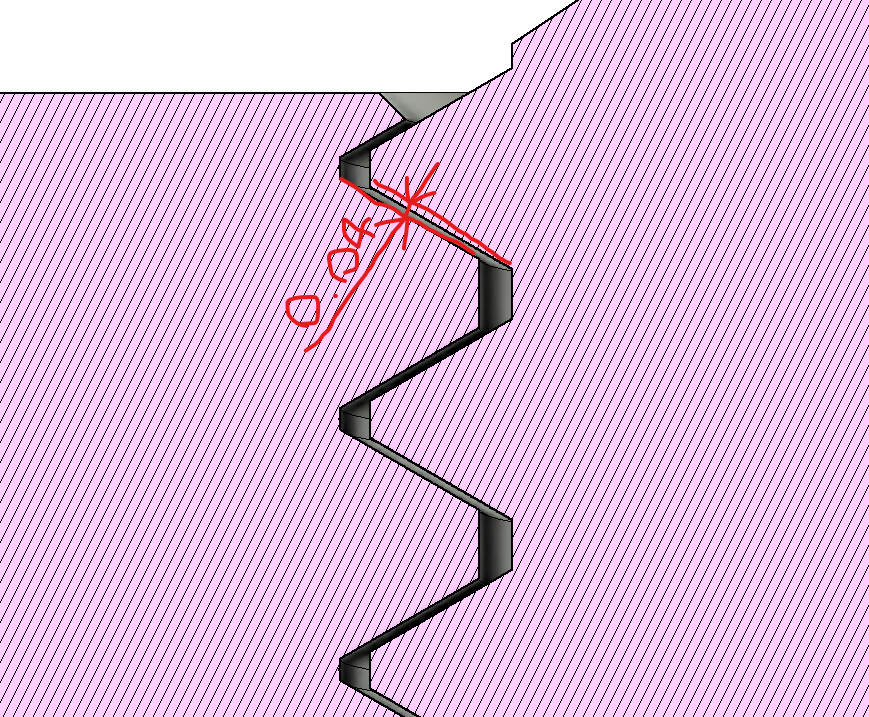
このまま造形するとそれぞれがサポート材付着分痩せるので、隙間が0.1~0.2mmぐらいになると想定されます。
0.1の隙間と聞くと、大したこと無いのでは?と感じるでしょう。しかし、こういった勘合部品の0.1mmって意外とガタツキがわかるレベルだったりします。
この標準状態からどれぐらい大きくすればいいかチェックしていきたいと思います。
今回下の画像で緑の線を引いた部分をオフセットさせて大きくしていきます。
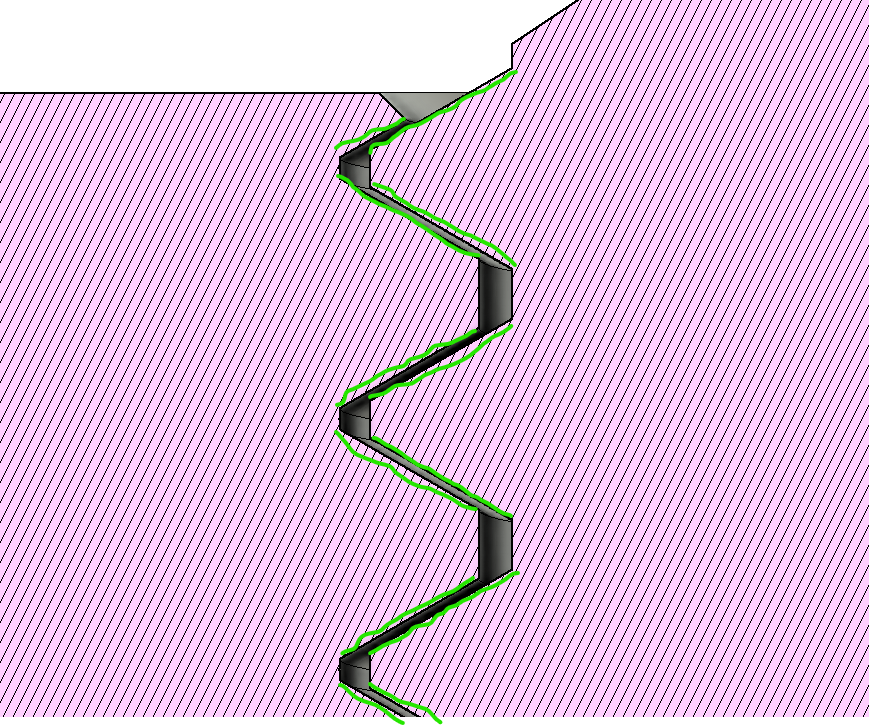
それぞれを+0.01、+0.02、+0.03、+0.05という4種類データを作り、造形してみました。
右側にあるのが雌ネジ、左手前はねじ込み治具、その治具の奥に雄ネジを造形しています。
色の濃い黄色の部分がサポート材になります。
ちょっと画質が粗くて見づらいのですが、それぞれサポート材に埋まった状態で出来上がります。
アジリスタのサポート材は水溶性なので、半日ほど水に漬けておけば溶けてモデル材のみが残ります。
水分をふき取り、しっかりと乾燥させれば造形完了です。
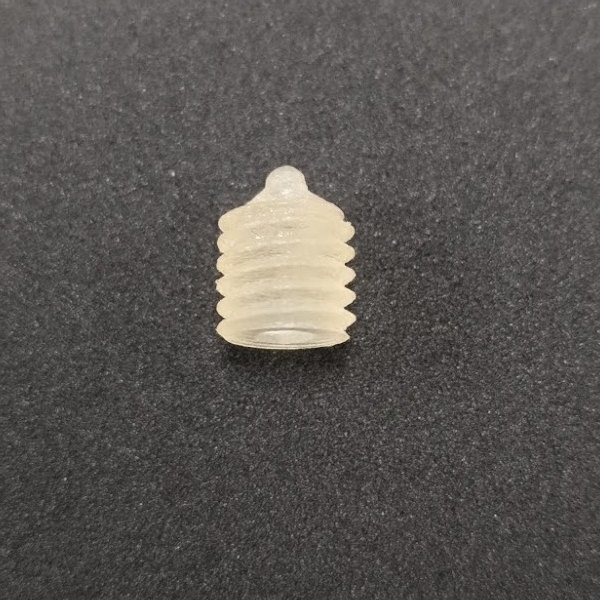
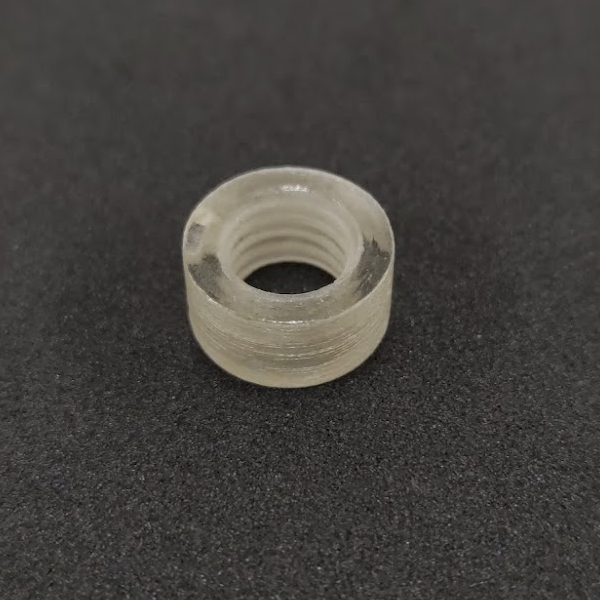
出来上がったものはこんな感じです。実際に勘合するこうなります。
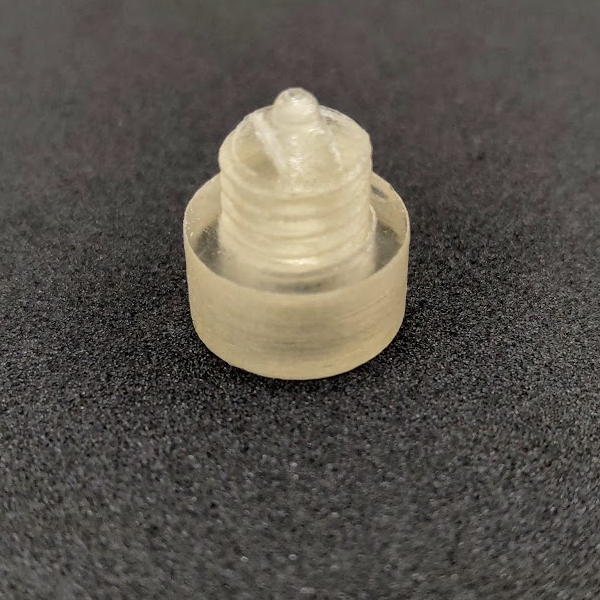

標準、+0.01、+0.02、+0.03、+0.05をそれぞれ勘合させてみました。
【標準】
スムーズに勘合ができるが、市販されているボルトナットと比較してガタツキが大きく感じる
【+0.01】
こちらもスムーズに勘合が出来る。標準よりはガタツキが減ったが、まだガタツキを感じる
【+0.02】
市販されているボルトナットの勘合感に近い。ガタツキも抑えられている。
【+0.03】
勘合時やや引っ掛かりを感じる。ガタツキ感はなくなった。
【+0.05】
勘合で明らかに引っ掛かりを感じる。無理やり勘合している感覚がある。
という感じでした。
今回、造形品をカットして寸法計測まで行ったわけではないため、あくまでも作業時の感覚でのお話となります。
結果としては、ネジ部のデータは標準から+0.02~0.03mmオフセットして大きくしておけば、勘合時のガタツキが抑えられるということがわかりました。
勘合時の干渉を考えると0.02mmがベストかなという感じなので、今後こういった勘合させるネジがある場合、データの時点で0.02mmほど大きくして造形用にSTLデータ化することで、勘合精度の良い造形物を作ることが出来そうです。
こういった細かい調整が必要な場合もありますので、3Dプリンタの方式や機械の個体差を実験を行って知ることで、次の造形をより良いものにすることが出来ます。
この後はもう少し掘り下げて考えてみたいと思いますので、そこまで興味ないよという方はこのあたりで終了していただいて大丈夫です。
今回も読んでくださりありがとうございました。
それではもう少し考察してみましょう。
今回、造形方向に対してネジを垂直方向にして作りました。そのため、ネジ山を下から積み重ねるように造形しています。
アジリスタだと造形ピッチが0.02mmなので、中心でカットして断面を見るとネジの山、谷は0.02mmの段差状になっています。
かなり抽象的に表すとこんな感じです。黄色がボルト側ネジの山、緑がナット側ネジの谷、水色がサポート材だと思ってください。
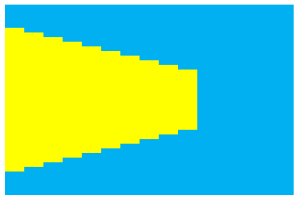
ボルト側
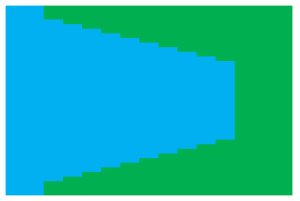
ナット側
アジリスタはUV硬化樹脂と水溶性サポートをインクジェットヘッドから直接塗布して造形します。
そのため、各層のモデル材とサポート材の間はこんな状態になっているます。
ですが、実際はモデル材とサポート材の境界面でそれぞれが混ざってしまうため、半硬化した物質が出来てしまいます。
オレンジ色の部分がそういった部分になります。
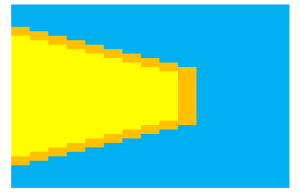
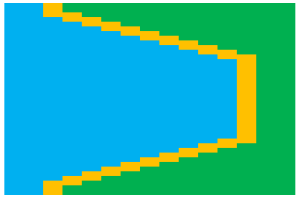
こういった部分が出来てしまうので、実際の造形物がデータに比べて痩せて(小さくなって)しまいます。
今回の実験ではこのオレンジの部分が発生することを考慮した上で造形データを作成するにはどれぐらい大きくすればよいのかを探りました。
こういった情報を把握しておくことで、勘合部品を造形した際の嵌めあいが良くなり、品質向上につながります。
アジリスタの場合、造形方向やサポートの付き方によって造形物とデータの差が±0.05~0.2程発生します。
こういった実験はお使いの3Dプリンタの特性や個体差で変わってくる部分なので、確認のためにやっておいて損はありません。
造形ピッチ(1層辺りの高さ)を調整できる場合は、それぞれでどれぐらいの誤差が発生するのか把握しておくと、造形物の形状や用途に合わせてピッチを選択できるようになり、造形不良が減ると思います。
インクジェット方式、マテリアルジェット方式、バインダージェット方式、光造形方式に関しては、今回の様に表面に半硬化樹脂が発生するので、その分を考慮して造形データを作成することが必要となります。ですが、これらの方式は比較的に造形ピッチが細かいので、そこまで敏感に考慮しなくてもいい場合もあります。
しかし、造形可能最小幅や最小径がありますので、その辺りは考慮する必要があります。大きな建造物や設備などの縮小モデルを作る場合、縮小したことで、形状がつぶれてしまい最小幅を下回ってしまうと造形できないので注意が必要です。
材料押出法(FDM/FFF)では、熱可塑性樹脂を使用するので熱収縮が発生します。収縮分を考慮しなければフィッティングの良い造形物を作ることは難しいです。しかし、材料毎の収縮率の違い、プリントヘッドや造形プレートの温度、更にプリンタ周辺の温度、湿度なども影響するため、収縮率を完全にコントロールするには温度や湿度を調整できる専用の部屋を準備する必要があります。なので、ネジの造形もできないことはありませんが、そういった細かな造形精度が求められるものは無理やりFDMで造形するよりも、上記の方式で出力した方が良いと言えます。しかし、収縮することを知っておかないと、簡単な箱状の造形物でもちゃんと閉まらない場合や組み立てできない場合もあります。なので、勘合隙間をあらかじめ大きめに設定しておくことで、収縮しても大丈夫な設計を行うことが大事です。
インターネット上には3Dデータを公開しているサイトもたくさんありますので、そういったサイトから造形用データをダウンロードすることもできますが、そのデータがプリント可能なのか事前にチェックすることが大事です。家庭用で販売されている3Dプリンタには、精度があまりよくないモデルもありますので、ご自身の持っているプリンタの造形精度と相談が必要になる場合もあります。
弊社の3Dプリントサービスでは、持ち込みデータはもちろん、データ作成から承ります。
持ち込みデータの場合、形状の欠落や造形不良になりそうな箇所が無いかチェックを行います。
修正が必要な場合、修正案をご提示させていただきます。お客様自身での作業が難しい場合もご安心ください。
弊社で作業を代行することもできますので、お気軽にご相談ください。
詳しくは3Dプリントサービス、ならびに3Dデータ作成サービスをご覧ください。
それでは、ここまで読んでいただき、誠にありがとうございました。
By M.I
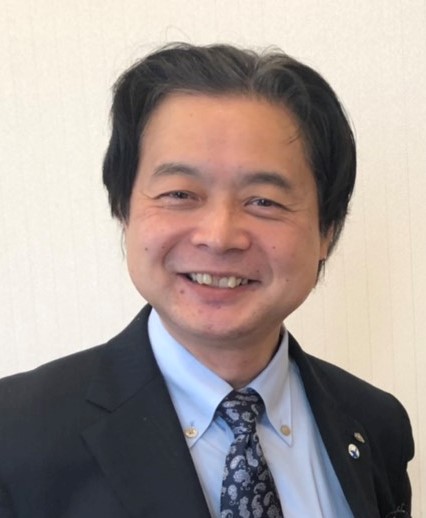
岸 竜也 (きし たつや)
株式会社キシテック 代表取締役
3Dプリンターを使ったモノづくりを提案しています。
機械設計を生業としてきたため、設計力に自信があります。
様々な分野から、試作品等の依頼を受け、製品化のお手伝いを多数してきました。
手書きの絵から、3Dデータを起こして、3Dプリントすることも。
自身も設計のみならず、機械加工、機械板金加工、溶接などのモノづくりを経験してきた実績があり、いろいろモノづくりを相談出来ます。
現在は石川県工業試験場様や、ISICO(石川県産業創出支援機構)様、JAIST(北陸先端科学技術大学院大学)様、石川工業高等専門学校様などと、繋がり多方面での対応が可能です。