【方式別紹介】必要なところに必要な機能を追加できる?指向性エネルギー堆積法
おはようございます、こんにちわ、こんばんわ
【方式別紹介】シリーズも第9弾ですね。
今回は「指向性エネルギー堆積法」について掘り下げていきます。
指向性エネルギー堆積法
指向性エネルギー堆積法(DED)は
溶かした金属材料を集積させて造形する方法です。
金属3Dプリンタの方式としては、パウダーベット方式同様に
主流な方式の為、多くのメーカーで採用され、
様々な機種が販売されています。
海外メーカーではTRUMPF、BeAM、InssTek他
たくさんのメーカーからリリースされています。
国内メーカではOKUMA、マザック、DMG森精機、
ニコンなどから販売されています。
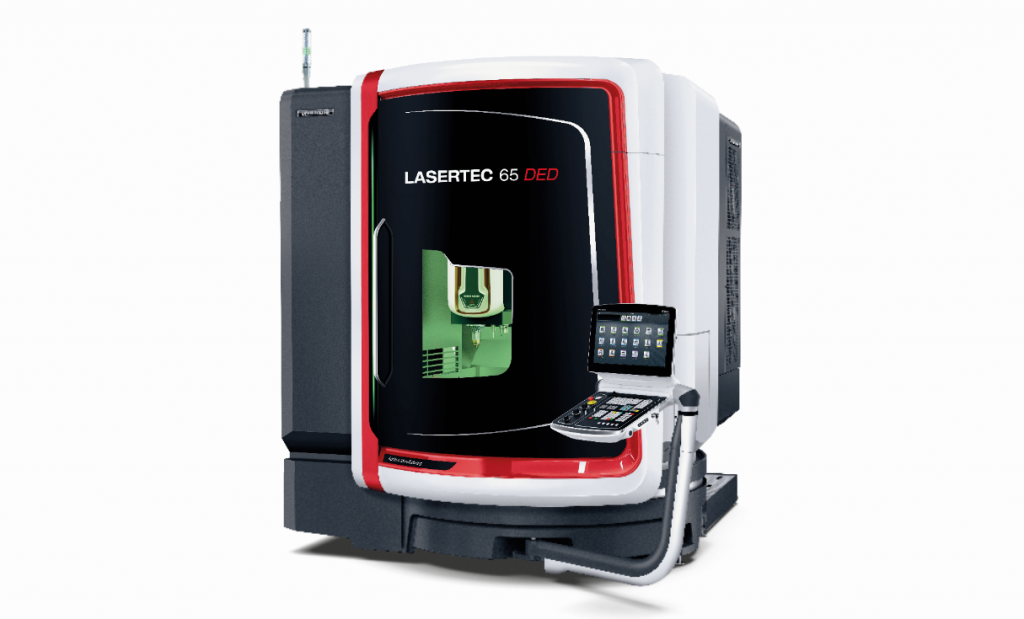
DMG 森精機社製 LASERTEC 65 DED
BeAM社製作のDED解説動画
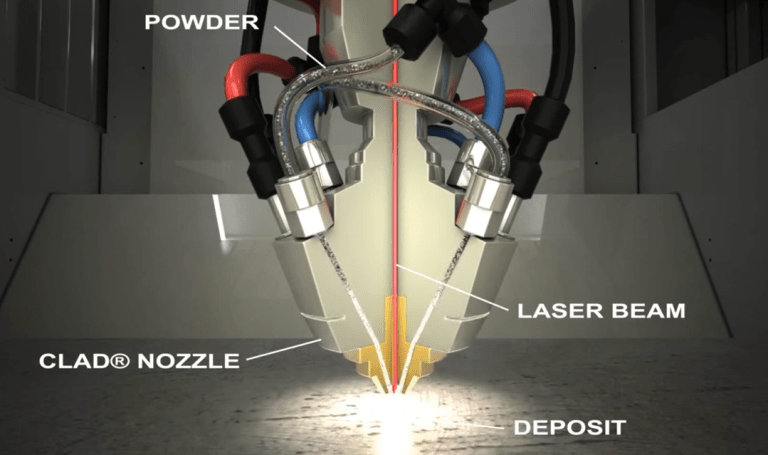
画像は動画からの抜粋となります。
指向性エネルギー積層法はノズルの中心から熱源となる
レーザーや電子ビームを照射して対象部分に溶融池をつくり、
そこへ金属粉末とシールドガスを噴射することで、
金属粉末を溶かし込んで造形していきます。
X、Y、Z軸の長さを変えるだけで簡単に大型造形物まで対応可能です。
また、バーチカルテーブルを使うことによって様々な方向から
造形が出来るので効率良く、高速で造形が可能です。
機種によっては、金属粉末の供給経路を切り替えることで、
複数の金属の積層を可能にします。
「それに何のメリットが?」となる方もいると思います。
従来の金属加工品は
・金属の塊を削り出して作る(切削加工)
・金属板をつなぎ合わせて作る(溶接)
・溶かした金属で形を作る(鋳造)
などの方法で製造します。
そして、金属加工で広く使われるのが鉄です。
鉄の融点は1500℃程と高く、密度も高いので重たいです。
逆に軽い金属といわれてイメージするのはアルミではないでしょうか。
アルミニウムの融点は約600℃程、鉄と比べてとても低いです。
この2つの材料を溶接で繋ぎ合わせるのは溶ける温度が違い過ぎる為、
とても難しいです。特殊なツールを使えば可能ですが、単純に溶接すると
接合境界面に不安定な金属化合物が生まれてしまい、わずかな衝撃でも
簡単に割れてしまうため、鉄材とアルミニウムはボルトで締結します。
ですが、DED方式では金属粉末を混合するのではなく、
それぞれを切り替えて積層することで、材料同士の境界を無くし、
強度が確保された造形物を作ることが出来ます。
その為、100%鉄材では重くてNGであったり、アルミニウム100%では
強度がNGといった場合でも、適した配合率で造形物を作ることで、
強度を保ちながら軽量な部品を作ることも可能になります。
DED方式は「レーザークラッディング」という技法が出来ます。
このレーザークラッディングとは金属部品の摩耗した部分に肉盛り補修を
行う技術のことを言います。金属部品の表面へ異なる金属で
コーティングを行うこともできるため、耐摩耗性の高い材料を
部品表面へコーティングしたり、焼き付き防止を行うこともできます。
古い機械で替えの無いパーツを修復したり、長期間使用されている金型の
補修が出来るなど活躍の場が広がっています。
DED方式はパウダーベット方式の様に不要な材料の除去作業も無いので
より効率的に造形物をつくることができます。
また、材料となる金属粉末の大きさや形状もパウダーベット方式より
制限が少ないので、比較的安価な粉末材料を使用することも出来ます。
「金属部品の補修やコーティングが出来る」、「異種金属でも積層が可能」、
「造形後の手間が少ない」、「比較的安価な材料も使える」と聞くと
前述のパウダーベット方式よりも優れているように聞こえますが、
指向性エネルギー堆積法ではFDM方式同様に、一筆書きの様に造形します。
そのため、DED方式は積層痕が残りやすいといった点があり、
再現性、寸法精度の面ではパウダーベット方式の方が優れいています。
この「再現性」という点ですが、
パウダーベット方式では造形する元データとの差であったり、
同じ形状を同時に複数個造形する場合の個体差が小さいです。
使用する材料粉末のサイズや積層ピッチが小さいので、
同じ形状を量産する上ではパウダーベット方式の方が向いているといえます。
では、DED方式はどういった分野に向いているかですが、
航空宇宙産業や医療材料の分野で活躍しています。
NASAでは、積極的に3次元積層造形(AM)技術の開発を進めている。
2020年6月にはDED方式の金属3Dプリンタを用いて
大型で複雑なロケットエンジンノズルを製造したと発表している。
発表によると、直径約1m、高さ約0.9mのエンジンノズルで
内部に冷却回路を備えており、構造も非常に複雑なため、
従来の溶接法や加工法で製造すると1年程かかるところを、
約1か月と記録的な速さで製造することができたそうだ。
この他、直径約1.5m、高さ約2.1mのエンジンノズルを
製造・評価しているという。今後は燃焼試験などで
耐久性と性能を実証していくという。
参照ページ
NASA、大型で複雑な構造のロケットエンジンノズルを3Dプリント
医療材料では、コバルトクローム合金製の歯冠が製作されています。
患者の歯の形状に合わせた歯冠を作ることが出来る為、
歯冠をかぶせる歯や周辺の歯に無理な力を及ぼさない
という利点があるそうです。
その他、患者ひとり一人に合わせた補助器具の製作といった場面でも
クロム合金やチタン合金とった生体適合材料を用いた造形品が活躍しています。
指向性エネルギー積層法を用いた金属3Dプリンタは、
それがメインというよりは、複合加工機の機能の一つとして
各メーカーから販売されている場合が多いです。
そのため、機械本体の価格は数億円規模のものがほとんどです。
展示会以外でこういった大型で高価な設備を見る機会は無いので、
自分も機会があればこういった機械を間近で見れたらいいなと思っています。
さて、なかなかに色々と書き連ねたので
そこそこボリュームがある記事になったと思います。
最後まで読んでくれている方が居るのか不安ですが、
今回はこの辺りで終わりたいと思います。
次回は金属3Dプリンタにおける「FDM方式」について
纏めていきたいと思います。
それでは、ここまでのご愛読ありがとうございました。
By M.I
次回の記事はこちら
前回の記事はこちら
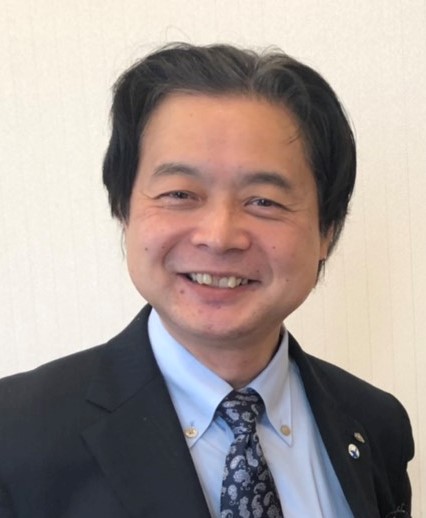
岸 竜也 (きし たつや)
株式会社キシテック 代表取締役
3Dプリンターを使ったモノづくりを提案しています。
機械設計を生業としてきたため、設計力に自信があります。
様々な分野から、試作品等の依頼を受け、製品化のお手伝いを多数してきました。
手書きの絵から、3Dデータを起こして、3Dプリントすることも。
自身も設計のみならず、機械加工、機械板金加工、溶接などのモノづくりを経験してきた実績があり、いろいろモノづくりを相談出来ます。
現在は石川県工業試験場様や、ISICO(石川県産業創出支援機構)様、JAIST(北陸先端科学技術大学院大学)様、石川工業高等専門学校様などと、繋がり多方面での対応が可能です。