【方式別紹介】金属粉末×ビーム光線で造形?パウダーベット方式
おはようございます、こんにちわ、こんばんわ
3Dプリンタのあれこれ 第8弾ということで前回の予告通り
パウダーベッド方式についてもう少し掘り下げていきます。
<パウダーベット方式>
Sodick社製 OPM250Lによる
遊星歯車装置(プラネタリーギア)の造形の様子
樹脂3Dプリンタの”粉末焼結積層造形”と同じ様に
10μm~60μmの球形の金属粉末を機械的に敷き詰め、
敷き詰めた金属粉末にレーザーや電子ビームを照射して
必要な部分を溶かして固めていく方法です。
積層ピッチは20μm~50μm程、敷き詰め~溶融を繰り返して
積層造形する為、造形品は固化していない粉末の中に埋もれながら
完成していきます。
造形完了後は、固化していない金属粉末を除去する作業が必要です。
尚、除去した粉末は遠心分離機やふるいにかけて、
不純物や中途半端に固化した粉末等を取り除かれて再利用されます。
固化していない粉末に埋もれて造形されますが、形状によっては
オーバーハングしている部分にサポート材という補助剤が必要となり、
それらを除去する工程も必要となります。
以前、こちらの記事(金属3Dプリンターで造形に挑戦!)でも触れましたが、
出来上がった造形物は表面が粗く、そのままで使うには難しいので、
ショットピーニング処理等の表面処理が必要です。
実際、金属部品は加工後に表面処理を行うのが当たり前なので
金属3Dプリンタ造形品が特別ということはありません。
酸化被膜で覆うことで劣化を防いだり、塗装することで表面を保護したりと
何かしら表面処理を行います。
パウダーベット方式は、現在の金属3Dプリンタ市場で
一番メジャーな方式なので、多くのメーカーで
この方式を採用した機種がリリースされています。
海外メーカーではEOS、3D Systems、SLM Solutions、TRUMPF、
その他、多くのメーカーでリリースされています。
国内メーカーでは上の動画にありますSodick、松浦機械製作所、
DMG森精機、三菱電機、アスペクトなどからリリースされており、
複合加工機としてレーザーでの焼結+端面処理等のツール加工を行える
ハイブリット金属3Dプリンタも多く販売されています。
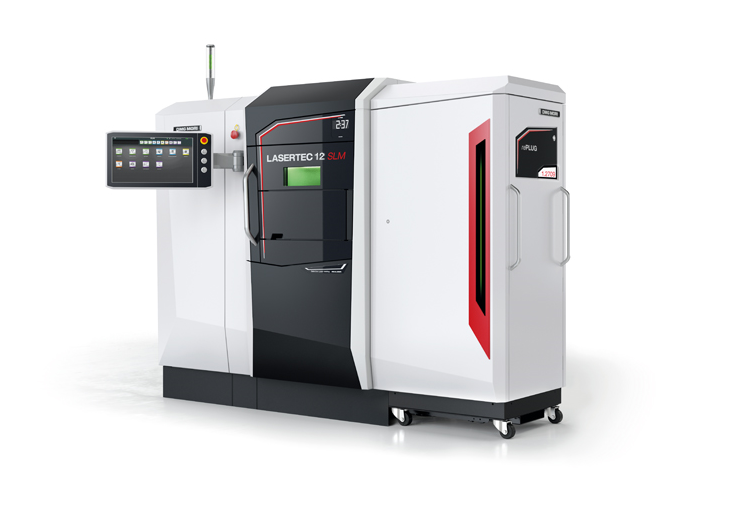
また、レーザーではなく電子ビームを用いたモデルをArcamという
海外メーカーがリリースしています。
電子ビームはレーザーと比べ造形速度が速く、チタン造形では
他社の設備ではできないサイズの造形が可能ということで、
航空宇宙産業の分野で活躍している様です。
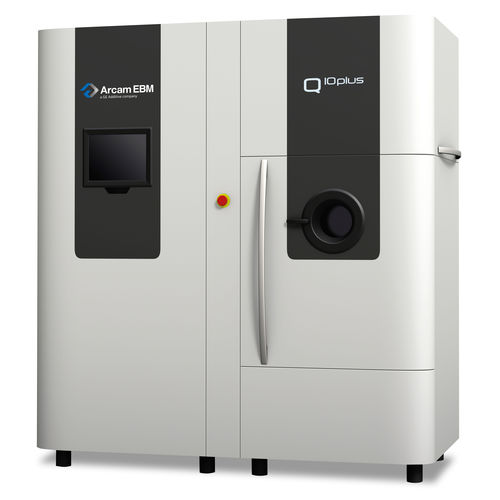
パウダーベット方式のメリットは「再現性の高さ」、「寸法精度の高さ」です。
デメリットは「造形範囲が限られる」、「造形時間が長い」といった部分です。
このデメリットに対して、複数のレーザーを搭載することで造形範囲を
広げたモデルや高出力レーザーを用いることで、造形速度を上げたモデルも
登場しています。
但し、現状ではレーザーの複数搭載や高出力レーザーは高価になる要因なので、
そういったモデルはハイエンドモデルとして販売されている様です。
パウダーベット方式で造形可能な金属は、
マルエージング鋼、ステンレス(SUS316L)、インコネル718、
インコネル625、コバルトクローム、アルミニウム(AlSi10Mg)、
チタン合金といった金属材料が使えます。
貴金属として良く使われる金・銀・プラチナといった材料や真鍮や銅などは、
まだパウダーベット方式では使用できません。
今後、レーザー出力の更なる向上や、材料となる金属の粉末の微細化が進めば
使用できる金属の種類も増えていくと思われます。
ここからは私の主観的な意見ですので、読み飛ばしていただいても大丈夫です。
このパウダーベット方式の金属3Dプリンタは、
これからの射出成型の分野に必要な技術だろうと勝手に思っています。
射出成型とは、金型を用いた成形法の一つで、
プラスチックなどの材料を加熱して溶かし、金型に送り込んだ後、
冷やすことで目的とする成形を行う手法です。
現在、射出成型で使う金型を作る流れは
①金型用の原型を作る
②原型を基にシリコンを使って型(A)をつくる
③シリコンの型(A)をつかって、セラミックの型(B)をつくる
④セラミック型(B)を基に、金属型(C)を作る
という流れで製作します。
原型と同じものを作るための金型を作るまでに
2つの型を製作する必要があります。
また、金型の冷却のための水管を加工する必要があり、
現在はドリルによる直線的な加工で行われています。
その為、入り組んだ部分へ水管を加工するのが難しく、
冷却の際にムラになってしまい、収縮率の計算が
難しくなるといった問題もあります。
こういった金型製造の手間や冷却用水管のレイアウト問題を
改善することに金属3Dプリンタは大いに役立つと思います。
まず、原型をデータ化することで、
原型のデータを基にした金属型の設計を直接行うことが可能となります。
さらに、水管のレイアウト最適化も同時に設計することが出来るので、
金型設計に掛かるLTの短縮が見込めます。
シリコン型やセラミック型を作る手間が減るため、
LT短縮やコスト削減につながります。
また、水管のレイアウト最適化によって
成形不良が少ない金型を作ることが出来る為、
材料ロスも少なくなり、長期的なコストメリットも見込めます。
「3Dプリンタによる最終製品の製造」も重要な観点ですが、
「3Dプリンタによる煩雑工程の改善」も重要な観点の1つと思います。
世の中にある製品の多くはプラスチックパーツを使っています。
”プラスチックパーツを大量生産できる3Dプリンタ”も必要な技術と思います。
ですが、大量生産という観点ではパーツ自体を作れる3Dプリンタよりも
”プラスチックパーツを作るための金型を短時間で作る3Dプリンタ”が
重要になってくると思います。
原型をデータ化し、最適な金型を3次元CADで設計を行い、
金型自体を金属3Dプリンタで出力することで、
量産に最適な金型を短期間で作ることが可能となります。
造形した金型を用いて射出成型という従来の技術でパーツを製造を行うことで、
3Dプリンタで直接パーツを作るよりもコストを抑えることが出来ると思います。
もちろん、これからの世の中は汎用品を大量生産する時代から
個人に合わせた専用品を少量多品種生産する時代に変わっていくと
言われています。ですが、専用品の全てがスペシャルパーツかと言われれば
単純なパーツは大量生産の対象と思います。
めまぐるしく変わる市場に合わせて、臨機応変に対応できるモノづくりの
強い味方として、既に航空宇宙産業や医療、自動車業界で3Dプリンタが
活躍していることからも、これからのモノづくりの中心になっていく可能性は
十分にあると思います。
さて、パウダーベッド方式について、前回の補足や個人的見解を入れながら
記述してきましたが、結構なボリュームになりましたね。
今回はこの辺りで終わりたいと思います。
次回は「指向性エネルギー堆積法」をクローズアップしていこうと思います。
それでは、ここまでのご愛読ありがとうございました。
By M.I
次回の記事はこちら
前回の記事はこちら
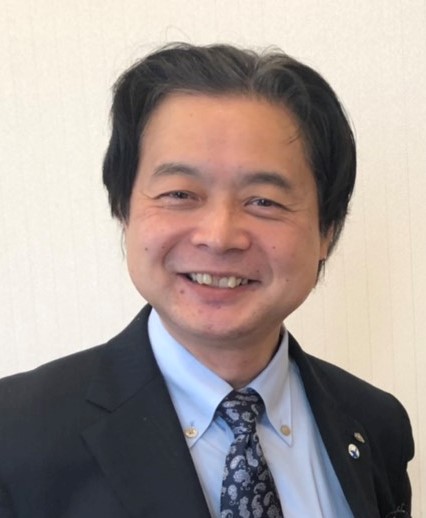
岸 竜也 (きし たつや)
株式会社キシテック 代表取締役
3Dプリンターを使ったモノづくりを提案しています。
機械設計を生業としてきたため、設計力に自信があります。
様々な分野から、試作品等の依頼を受け、製品化のお手伝いを多数してきました。
手書きの絵から、3Dデータを起こして、3Dプリントすることも。
自身も設計のみならず、機械加工、機械板金加工、溶接などのモノづくりを経験してきた実績があり、いろいろモノづくりを相談出来ます。
現在は石川県工業試験場様や、ISICO(石川県産業創出支援機構)様、JAIST(北陸先端科学技術大学院大学)様、石川工業高等専門学校様などと、繋がり多方面での対応が可能です。